Anforderungen für die Vorbehandlung von Flotationstanks
United Pipelines Services AS entwickelt spezielle Lösungen für die Innenbeschichtung von Rohrsystemen und Laminierung von Tanks. Die Systeme und Verfahren des Unternehmens sind besonders für schwer zugängliche Bereiche in anspruchsvollen Arbeitsumfelder geeignet. United Pipelines Services, auch bekannt unter UniPiSe, kooperiert jetzt mit Teknos.
Diese Kundenerfolgsgeschichte wurde ursprünglich in dem norwegischen Magazin „Rust og Råte” für Oberflächenbehandlungen veröffentlicht.
Fachleute, die schon lange in der Branche tätig sind, wissen, dass ein effektiver Korrosionsschutz in Tanks nicht immer einfach ist. In der Schifffahrt haben Reedereien ständig mit verschiedenen Anforderungen an die Zuverlässigkeit zu kämpfen, von Ladetanks über Tanks für den Chemikalientransport bis hin zu Massengutfrachtern. Wir haben es mit großen und kleinen Tanklagern mit Chemikalien und aggressiven Produkten zu tun, die die Beschichtung nahezu zersetzen. In der Öl- und Gasindustrie auf See gibt es alle Arten von Lagertanks und Druckbehältern, die äußeren Einwirkungen sowie großen Flüssigkeitsmengen wie Schlamm, Öl, Korrosionsschutzmittel, Kühlwasser und dergleichen ausgesetzt sind.
Es ist oft einfacher, die Oberflächenbehandlung gemäß Anleitung während des Bauprozesses und bei der Herstellung der verschiedenen Tanks durchzuführen. Durch Sandstrahlen vorbehandelter Stahl, von Walzzunder gereinigt und frei von Fett und Schmutz sowie allen Korrosionsschutzmitteln. Ein guter Zugang sowie beheizte und beleuchtete Produktionsstätten helfen dabei, um die NORSOK-Norm einzuhalten.
Es muss auch alles gewartet werden und das Unternehmen hat viel Erfahrung damit, dass Theorie und Praxis in der Nordsee sehr unterschiedlich sein können. Arbeitsumgebung und Zugang sind hier anders. Die Luftfeuchtigkeit ist hoch, die Temperatur niedrig, der Salzgehalt maximal, die Sicht für das Sandstrahlen schlecht, der Staub und der Schleifabfall eine Herausforderung. Der Zeitfaktor hinsichtlich einer Betriebsunterbrechung und der Wunsch nach einem optimalen Korrosionsschutz konkurrieren miteinander.
Wir haben uns ein Projekt von Statoil bei einer seiner Anlagen näher angesehen. In der Anlage sind Flotationstanks erheblichen Einwirkungen ausgesetzt und es ist deshalb ein größerer Inspektions- und Wartungsaufwand als bei anderen Tanks notwendig. Dies ist teuer und anspruchsvoll in Bezug auf den Betrieb der Plattform. Außerdem wollte Statoil herausfinden, ob die Intervalle durch neue Maßnahmen verlängert werden können.
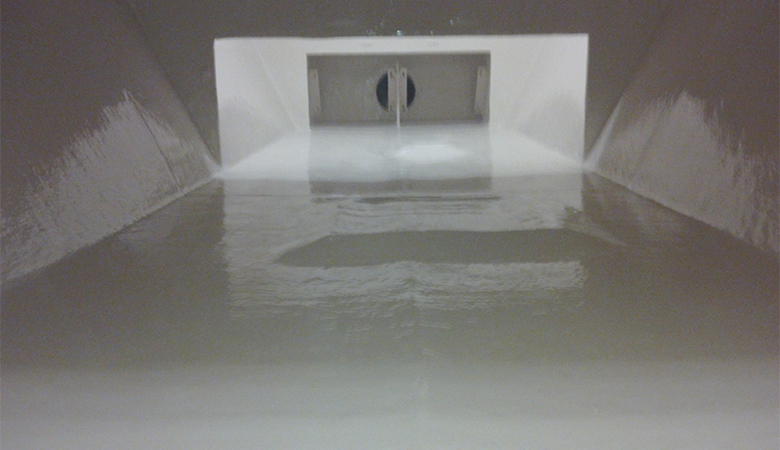
Die Flotationstanks mit vier Kammern.
Man entschied sich für UniPiSe AS, wo Rolf Wingsternes, Marketing/R&D Manager, und Carsten Færøy, technischer Leiter, seit vielen Jahren im Bereich Epoxid- und Laminatbeschichtungen tätig sind. Das Unternehmen hat sich in der Innen- und Außenbeschichtung von Rohrsystemen (Pipelines) an Land und See einen Namen gemacht. Es besteht nun auch eine Zusammenarbeit mit Teknos Oy, einem finnischen Unternehmen für Beschichtungsprodukte mit Produktionsstätten auf der ganzen Welt. Rolf und Carsten besprachen ihre Anliegen zunächst mit Teknos Oy und führten Tests in den Labors in Finnland durch, woraus sich eine Zusammenarbeit mit Teknos Norwegen ergab.
Wir fragten Carsten Færøy und den neu ernannten Leiter Robert Edward Babiak (Frosio Level 3), wie die Aufgabe definiert wurde:
Carsten: „Grundsätzlich war es nicht unsere Aufgabe, das Rad neu zu erfinden. Für uns war es wichtig zu sehen, wie die Beschichtung abgenutzt wurde und welche chemischen und physikalischen Einwirkungen während des Betriebs im Tank existierten.
Das Flüssigkeitsvolumen bestand hauptsächlich aus Schlamm, Öl, Wasser, Auswasch- und Korrosionsschutzmitteln, Reinigungsmitteln und Produktionschemikalien, also weniger aggressiven Flüssigkeiten.
Der nächste Schritt war, die physikalischen Einwirkungen wie Druck, Temperatur, Durchflussrate und mögliche Partikel aus Rohren und Verbindungen zu überprüfen. Aber auch hier lag alles innerhalb von Parametern, die für alle normal sind.
Dann ging es nur darum zu sehen, wie die Wartung vorher durchgeführt und die Abläufe während des Betriebs gestaltet wurden.”
Und dann kam die Antwort von alleine?
Carsten: „Ja, und dort lagen viele der Probleme! Die Tanks waren eng und relativ klein, es gab viele Düsen und geschweißte Verbindungsrohre, die den Zugang erschwerten. Sie befanden sich in Bereichen, die ungefähr der Lufttemperatur entsprachen wie sonst auf der Plattform, was den Taupunkt der Tanks während der Behandlung veränderte. Aufgrund von Durchdringungen und vielen Hohlräumen war es schwierig, die Stahlreinigung auf SA 2.5 durchzuführen. Es war eine Herausforderung, einen Salzgehalt unter 20 ml/m² zu erhalten. Dies wurde aber mit destilliertem Wasser erreicht, insbesondere zum Reinigen des Tankbodens.
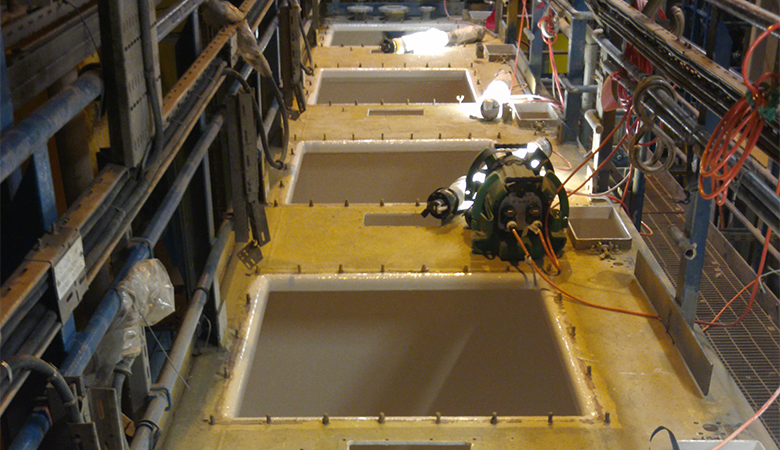
Alle Flotationstanks wurden mit destilliertem Wasser gewaschen.
Im Fall der aktuellen Beschichtung würden wir einen besseren mechanischen Schutz anstreben und dabei Epoxid verwenden, um die Flüssigkeitsströmung zu verbessern. Außerdem würden wir das Epoxid mit einem angepassten Laminat verstärken, das die Härte der Beschichtung deutlich erhöht und gleichzeitig genügend Flexibilität bietet.”
Und damit wurden alle Probleme gelöst?
Auf diese Frage gab uns Robert Edward Babiak, Leiter des Projekts, in seinem charmanten Polnisch-Norwegisch folgende Antwort:
Robert: „In diesem Industriezweig ist nichts einfach. Und die Standpunkte können häufig das Schlimmste sein! Meine Anforderungen an die Vorbehandlung waren anspruchsvoll und in Bezug auf die Umgebung vielleicht schwierig. Bei früheren Inspektionen stellten wir fest, dass der Salzgehalt auf der Oberfläche zu hoch war. Ich bat um erhitztes und destilliertes Wasser zum Reinigen, da nach dem Lackieren Wasser in den Boden des Tanks eindrang. Darüber hinaus war es sehr wichtig, die Trockenzeit zwischen den Schichten einzuhalten.
Glücklicherweise möchte Statoil lieber 10 m² richtig als 1.000 m² falsch behandelt haben. Wir wurden also großartig unterstützt, auch wenn der Zeitfaktor eine Rolle spielte.
Die Mitarbeiter des Wartungsunternehmers vor Ort verfügen über umfassendes Wissen und sie haben die Aufgabe mit der gleichen Tatkraft angepackt wie wir. Jedes Detail wurde sorgfältig überprüft und überwacht. Sie übernahmen alles in Bezug auf Sandstrahlen und Reinigen und UniPiSe die Grundierung bis zur Fertigstellung.
Wir haben eine Schicht Epoxidgrundierung und fünf Schichten Epoxid aufgetragen, mit zwei Schichten Laminat. Die Gesamtdicke betrug ca. 3 mm. An einigen Stellen war es anspruchsvoll, das Laminat in die Beschichtung einzuarbeiten. Insgesamt erreichten wir aber ein gutes Ergebnis über den gesamten Tank. Statoil wird nun den Tank inspizieren und in ihren 50 Anlagen gibt es mehrere Tanks mit den gleichen Herausforderungen.”
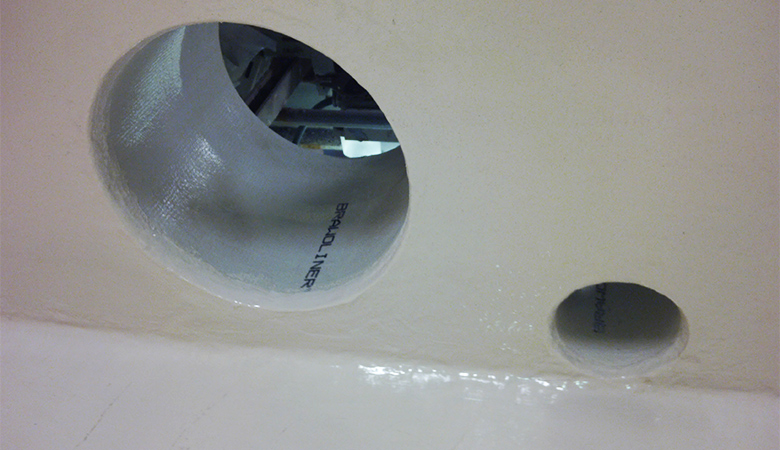
Die Verstärkung war bei der Gesamtumsetzung wichtig.
Rolf Wingsternescan fügt abschließend hinzu: „Wir hoffen, damit aufzeigen zu können, dass eine sorgfältig geplante und umgesetzte Wartung das A und O für ein gutes Ergebnis ist. Wenn wir bei der Umsetzung nachlässig sind, wird es auf lange Sicht sehr teuer. Das Spannende an einem Laminierungsprojekt ist, dass UniPiSe gleichzeitig Düsen und Ausformungen mit seiner beeindruckenden ULS High Temp-Lösung erneuert. Das heißt: Zwei Projekte mit einer Firma bringt Einsparungen für Kunden und beschleunigt die Umsetzung.”