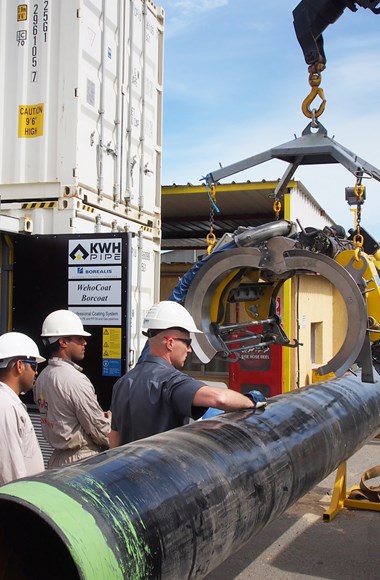
krav på förbehandling av flotationstank
United Pipelines Services AS utvecklar speciallösningar för innerfoder av rörsystem och lamineringstankar. Företagets system och metoder är särskilt anpassade för områden med svårtillgängliga och utmanande arbetsmiljöer. United Pipelines Services a.k.a UniPiSe samarbetar nu med Teknos.
Detta kundcase publicerades ursprungligen i ett norskt ytbehandlingsblad Rust och Råte.
Alla som har varit i branschen i några år är bekanta med problemet att effektivt bekämpa korrosion i tankar. I sjöfarten har rederier alltid kämpat med olika krav på tillförlitlighet, från lasttankar till kemikaliebehållare och containerfartyg. I branschen har vi stor och liten tanklagring av kemikalier och aggressiva produkter som nästan "äter" beläggningen. I olje- och gasindustrin till havs har vi alla typer av lagrings- och trycktankar som utsätts för yttre påtryckningar samt stora volymer vätska, såsom lera, olja, korrosionshämmare, kylvatten och så vidare.
Det är ofta lättare att utföra ytbehandlingen enligt boken under byggprocessen och vid tillverkningen av de olika tankarna. Att jobba med nytt sandblästrat stål, rengjort från vals hud och fri från fett och andra föroreningar. Med gott om utrymme och varma produktionsanläggningar följer du bara Norsok-standarden och alla är nöjda!
Men saker måste underhållas, och i Nordsjön har de gott om erfarenhet av att teori och praktik kan vara väldigt olika. Här är arbetsmiljön och tillgängligheten inte längre densamma. Fuktigheten är hög, temperaturen är låg, salthalten maximalt, utrymmet för blästring är dåligt, damm och slipavfall är en utmaning. Tidsfaktorn när det gäller stopp under drift och önskan om optimalt korrosionsskydd konkurrerar med varandra.
Vi har tittat på ett projekt som Statoil har prioriterat vid en av sina anläggningar där flotationstankar utsätts för stora belastningar och där kravet på inspektion och omfattande underhåll kan behövas mer frekvent än för andra tankar. Detta är dyrt och krävande för plattformens drift, och Statoil ville se om intervallerna kunde bli längre genom att vidta nya åtgärder.
Flotationstanken hade fyra kammare.
UniPiSe AS var det företag som valdes, där Rolf Wingsternes, Marknads- och R & D-chef, och Carsten Færøy, teknisk chef, har arbetat med epoxi- och laminatbeläggningar under många år. Idag har bolaget vuxit stort inom området inre och yttre beläggning av rörledningar (offshore / onshore). Företaget samarbetar nu med det finska företaget Teknos Oy, som är ett färgtillverkande företag med produktion över hela världen. Samarbetet började med att Rolf och Carsten delade med sig av sina åsikter och upplevelser med Teknos Oy och genomförde prov i sina laboratorier i Finland, vilket i sin tur resulterade i ett samarbete med Teknos AS i Norge.
Vi pratade med Carsten Færøy och den nyutnämnda handledare Robert Edward Babiak (Frosio level 3) om hur uppgiften specificerades.
Carsten: "I grund och botten var det inte vår uppgift att försöka uppfinna hjulet på nytt." Det som var viktigt för oss var att se hur sliten beläggningen blev och vilken kemisk och fysisk belastning det förekom i tanken under dess drift.
Innehållet var mestadels lera, olja och vatten, korrosionshämmare, rengöringsmedel och produktionskemikalier. Dvs. vätskor som inte var särskilt aggressiva.
Nästa steg var att titta på de fysiska påfrestningarna, såsom tryck, temperatur, flödeshastighet och eventuella partiklar från rör och anslutningar. Men även här var vi inom områden som inte "skrämde" någon.
Då handlade det bara om att undersöka hur underhåll utförts tidigare och hur förfarandet under driften såg ut."
Och därefter fick vi svaret automatiskt?
Carsten: "Det var här många av problemen låg, ja. Tankarna var trånga och relativt små, det fanns många munstycken och svetsade anslutningsrör, vilket gjorde dom svåråtkomliga. De befann sig i områden där temperaturen var samma som i luften eller på plattformen, vilket förändrade daggpunkten för tankarna under behandlingen. Det var svårt att utföra rengöring till SA 2,5 på grund av genomslag och många håligheter. Det var en utmaning att få en salthalt under 20 ml / m², men detta hanterades genom att använda destillerat vatten för tvätt, särskilt på tankens botten.
Tankarna tvättades med destillerat vatten.
När det gäller den faktiska ytbehandlingen bestämde vi oss för att använda ett bättre mekaniskt skydd, vi skulle använda epoxi som förbättrar vätskeflödet. Dessutom skulle vi förstärka epoxin med ett skräddarsytt laminat som ökade beläggningens hårdhet avsevärt, samtidigt som den fick tillräcklig flexibilitet. "
Och alla problem löstes?
Nu har vi kontaktat Robert Edward Babiak, som var handledare under operationen och med sin fina polska-norska kunde han rapportera följande:
Robert: "Ingenting är lätt i denna bransch, och attityderna – kan ofta vara dåliga! Det var inte alltid lätt eftersom mina krav på förbehandling var krävande och kanske svåra att anpassa till omgivningen. Vid tidigare inspektion fann vi att salthalten på ytan var för hög. Jag bad om uppvärmt och destillerat vatten för att tvätta med när vatten kom in på tankens botten efter att målningen hade slutförts. Dessutom var kravet på korrekt torkningstid mellan färgskikten väldigt viktig.
Lyckligtvis har Statoil en filosofi att de hellre har 10 m² som är korrekt ytbehandlat än 1000 m² felaktigt. Så där fick vi bra stöd , även om tidsfaktorn var viktig.
Underhållsleverantören hade personal med hög kunskap och de tacklade uppgiften med samma energi som vi gjorde. Varje detalj var noggrant inspekterad och övervakad. De gjorde allt avseende blästring och rengöring och UniPiSe gjorde allt från primer till färdigställande beläggning.
Vi applicerade ett lager epoxiprimer och fem skikt epoxi, med två lager av laminat längs vägen, en total tjocklek av ca. 3 millimeter. Det var en utmaning att rulla ut laminatet på vissa ställen, men totalt sett fick vi ett bra resultat i tanken. Statoil kommer nu att följa upp genom att inspektera tanken, och efter detta finns det många fler tankar på deras 50 anläggningar med samma utmaning."
Förstärkning var viktigt på alla implementeringar.
Rolf Wingsternescan ger sista ordet i frågan: "Vi hoppas att det här visar att omsorgsfullt planerat och genomfört underhåll är det allra bästa och ger ett bra slutresultat. Om vi är slarviga med genomförandet blir det väldigt dyrt i det långa loppet. Det som är bra med att använda laminering är att UniPiSe samtidigt renoverar alla munstycken och implementeringar med sin imponerande ULS High Temp-lösning. Det betyder: Två operationer som utförs av endast ett företag, vilket både sparar tid och pengar för kunden."
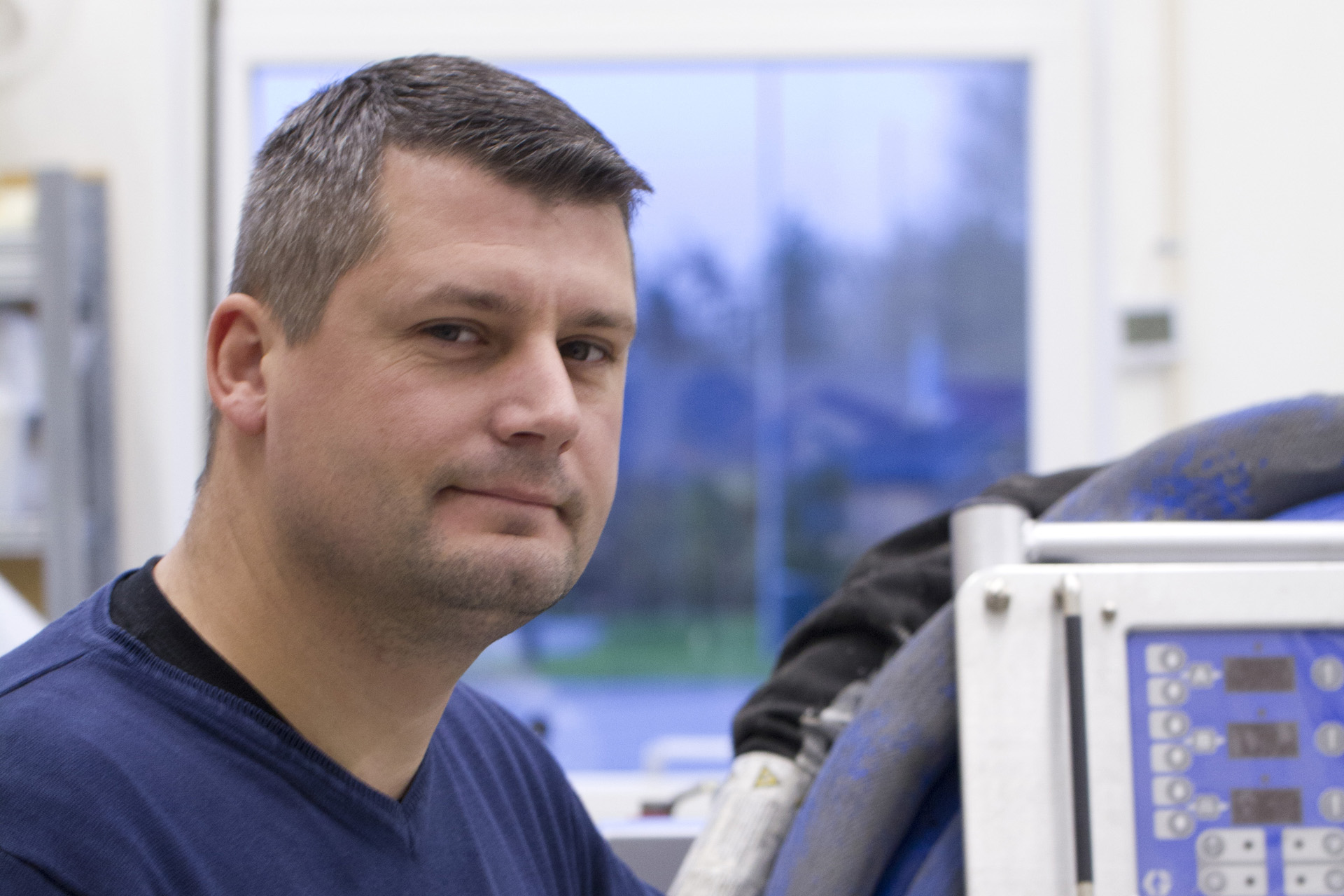
Vi hoppas att det här visar att omsorgsfullt planerat och genomfört underhåll är det allra bästa och ger ett bra slutresultat.
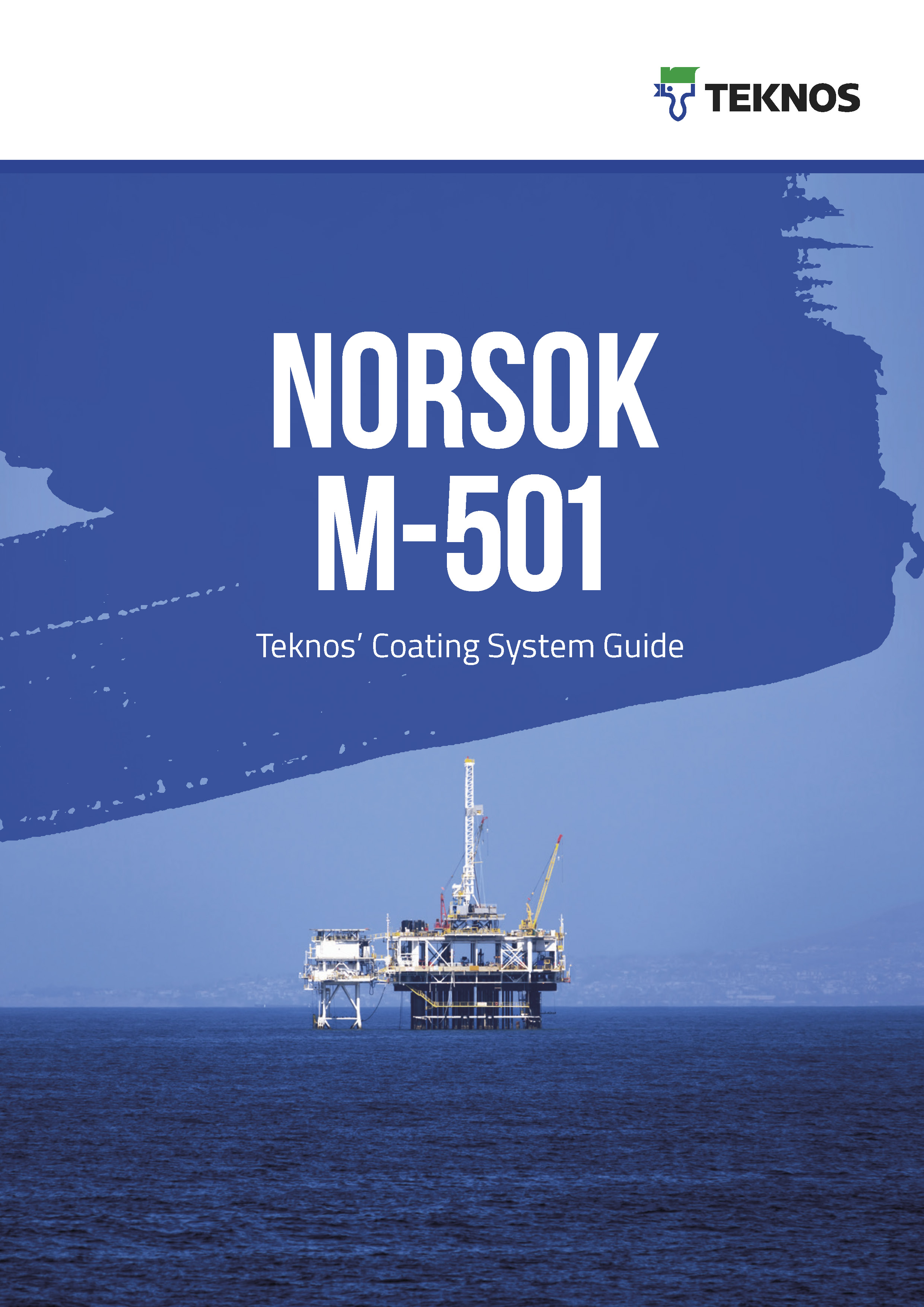
NORSOK M-501 Teknos coating system guide
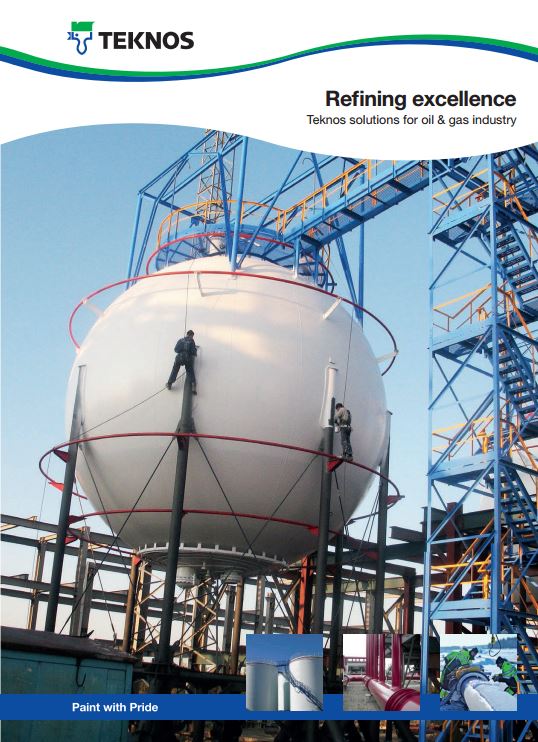
Teknos lösningar för olje- och gasindustrin
Är du intresserad av industriell målning? Registrera dig till vårt nyhetsbrev.