TEKNOPUR 300-800
Elastomeercoating
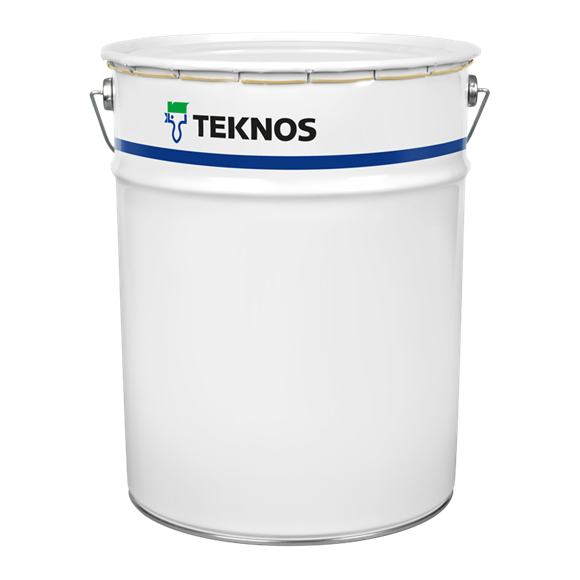
- Elastomeer
- Bestand tegen onderdompeling
- Slijtvastheid
- 2K, 2-component
TEKNOPUR 300-800 is een tweecomponenten, oplosmiddelvrije elastomeercoating. Coating wordt aangebracht door te spuiten. TEKNOPUR 300-800 is gebaseerd op op pure polyurea.
Bedoeld voor gebruik als afdichting van bitumen daken en betonconstructies en als coating voor oppervlakken die slijtvastheid vereisen, bijv. transportwagons. TEKNOPUR 300-800 is bestand tegen schokken, harde slijtage, chemicaliën en constante onderdompeling in water. Het hardt ook uit bij een temperatuur van -20 °C. Coating vergeelt onder invloed van UV-licht. Wanneer een oppervlak met een goed kleurbehoud gewenst is, moet het oppervlak worden overschilderd met bijv. TEKNODUR polyurethaan dekverf. De coating wordt meestal aangebracht tot een dikte van 500 - 3000 µm. Brandweerstandsklasse Efl voor vloeren. Voor objecten die worden blootgesteld aan chemische onderdompeling, wordt de kleur lichtgrijs aanbevolen. Het product heeft de CE-goedkeuring voor de bescherming van betonconstructies.
Technisch Informatieblad
Veiligheidsinformatieblad
Voorbereiding van het oppervlak
Applicatie
Applicatie voorwaarden
Opslagruimte
Vaste stof gehalte | circa 100 % in volume |
---|---|
Totale massa van vaste stoffen | circa 1120 g/l |
Vluchtige organische stoffen (VOS) | circa 0 g/l |
Verwerkingstijd | 5 sec. (+23 °C) |
Mengverhouding | 1:1 in volume (comp. A : comp. B) |
Verharder | Comp. A: TEKNOPUR HARDENER 7245 |
Glans | Glanzend |
Praktisch rendement | De waarden zijn afhankelijk van de aanbrengtechniek, de gesteldheid van het oppervlak, overspray, enz. |
Droogtijd - kleefvrij | Ca. 12 sec |
Droogtijd - geschikt voor licht verkeer | Ca. 40 sec |
Droogtijd - volledig uitgehard | Ca. 1 d |
Reinigen | TEKNOCLEAN 6496, TEKNOCLEAN 6481-00. |
Kleuren | Zwart, tegelrood, RAL 1023, RAL 7031, lichtgrijs en signaalgeel RAL 1003. Andere kleuren op afspraak. |
Veiligheidsmarkeringen | Zie het veiligheidsinformatieblad (SDS). |
Goedkeuringen & certificaten | CE marking |