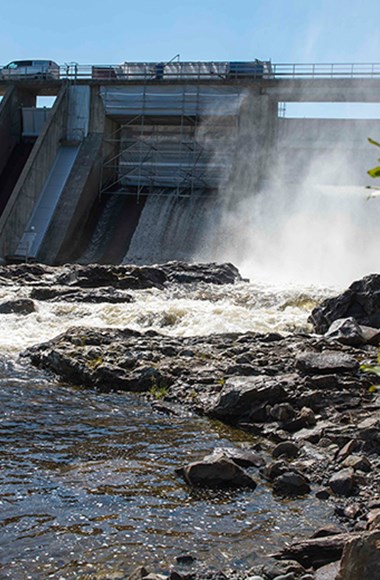
Coating Solutions for Hydropower Plants
Teknos’ full range of advanced, high-performance protective coatings protect the structures of an entire hydropower plant from corrosion.
Coatings for hydropower plant structures
Teknos coating solutions protect the structures of an entire hydropower plant from corrosion – both immersed and dry parts. TEKNOMASTIC 80 PRIMER, INERTA 160 and INERTA 165 are all examples of products with long-term track record in immersed use, for both steel and concrete constructions. The products have gone through rigorous laboratory testing.
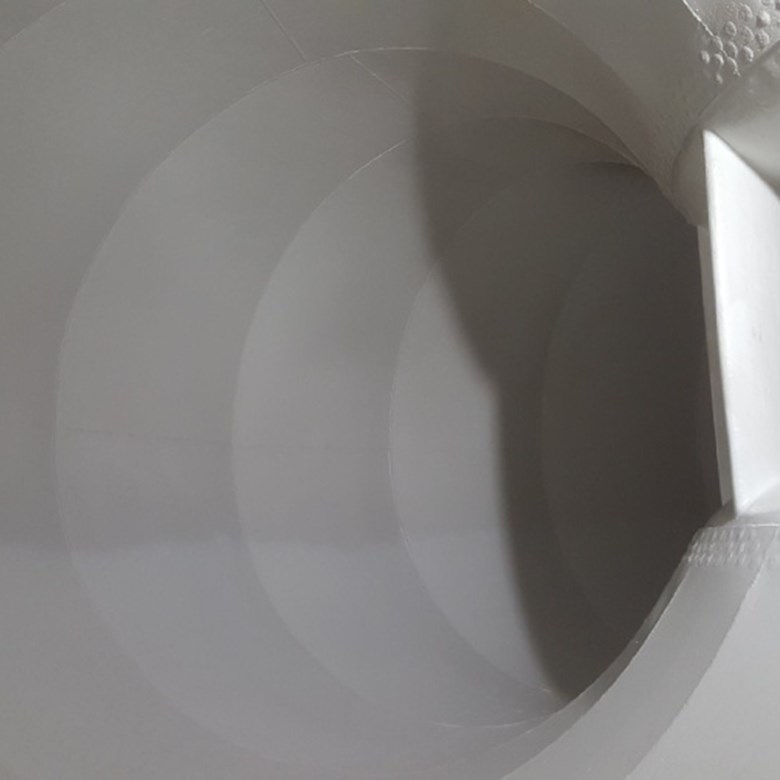
Teknos sustainable coating solutions
- High volume solids coatings of 82-96%
- Long maintenance cycles of even 40 years, depending on the selected coating system and environment
IMPORTANT CONSIDERATIONS WHEN COATING HYDROPOWER PLANT STRUCTURES:
- Thorough pretreatment with a rough blasting profile
- Surface cleanliness tests after pretreatment
- Protection of surroundings
- Harsh painting conditions with low temperatures and high/varying humidity
- Challenging reachability of structures
- Need for highly professional contractors
Coating new objects Maintenance painting Product details
CONSIDERATIONS WHEN COATING NEW OBJECTS
Hydropower plant structures, penstocks, gates as well as sluices have to withstand use even for decades. The structures are immersed or located in the splash zone and have to withstand mechanical and abrasive stress, such as flowing water itself as well as particles that come with the water flow. These factors make hydropower plants one of the toughest environments for coatings to serve.
CONSIDERATIONS WHEN REPAINTING HYDROPOWER STATIONS
The structures are complex to repaint; functions on the plant have to be stopped during maintenance and the structures are physically difficult to reach, handle, pretreat and paint. To make the maintenance cycle as long as possible, the paints need to be super durable and of high quality.
Product details
*In addition to the above-mentioned approvals, there are several approvals by country-specific requirements and standards, such as SILKO, ELFORSK, NS 5417 (Norwegian Hydropower std.), NORSOK M-501 etc. | ||||||
Product | VOC g/l | Vol. Solids % |
DFT range (µm) |
Pot life (min) |
Equipment requirements |
Approvals |
INERTA 160 | abt. 40 | 96 | 500 | 20 | 2K airless | Im 1, 2, 3 acc. ISO 12944-5, Abrasion resistance test |
The highest resistance against mechanical loads, including the effects of ice |
||||||
INERTA 165 | abt. 100 | 92 | 200-300 | 30 | 1K airless | Im 1, 2, 3 acc. ISO 12944-5 Abrasion resistance test |
Very good resistance against mechanical loads, including the effects of ice |
||||||
INERTA 165 TIX | abt. 100 | 92 | 250-600 | 30 | 1K airless | Im 1, 2, 3 acc. ISO 12944-5 Abrasion resistance test |
High film build version of INERTA 165 | ||||||
TEKNOMASTIC 80 PRIMER | abt. 200 | 82 | 80-230 | 120 | 1K airless | Im 1, 2, 3 acc. ISO 12944-5 Im 4 acc. ISO 12944-9 Abrasion resistance test |
Several NORSOK M-501 approvals, including systems 1, 3, 7A, 7B and 8A |
Teknos’ technical service professionals have vast experience in industrial painting and are happy to help you
Leave a contact request Find your local Teknos
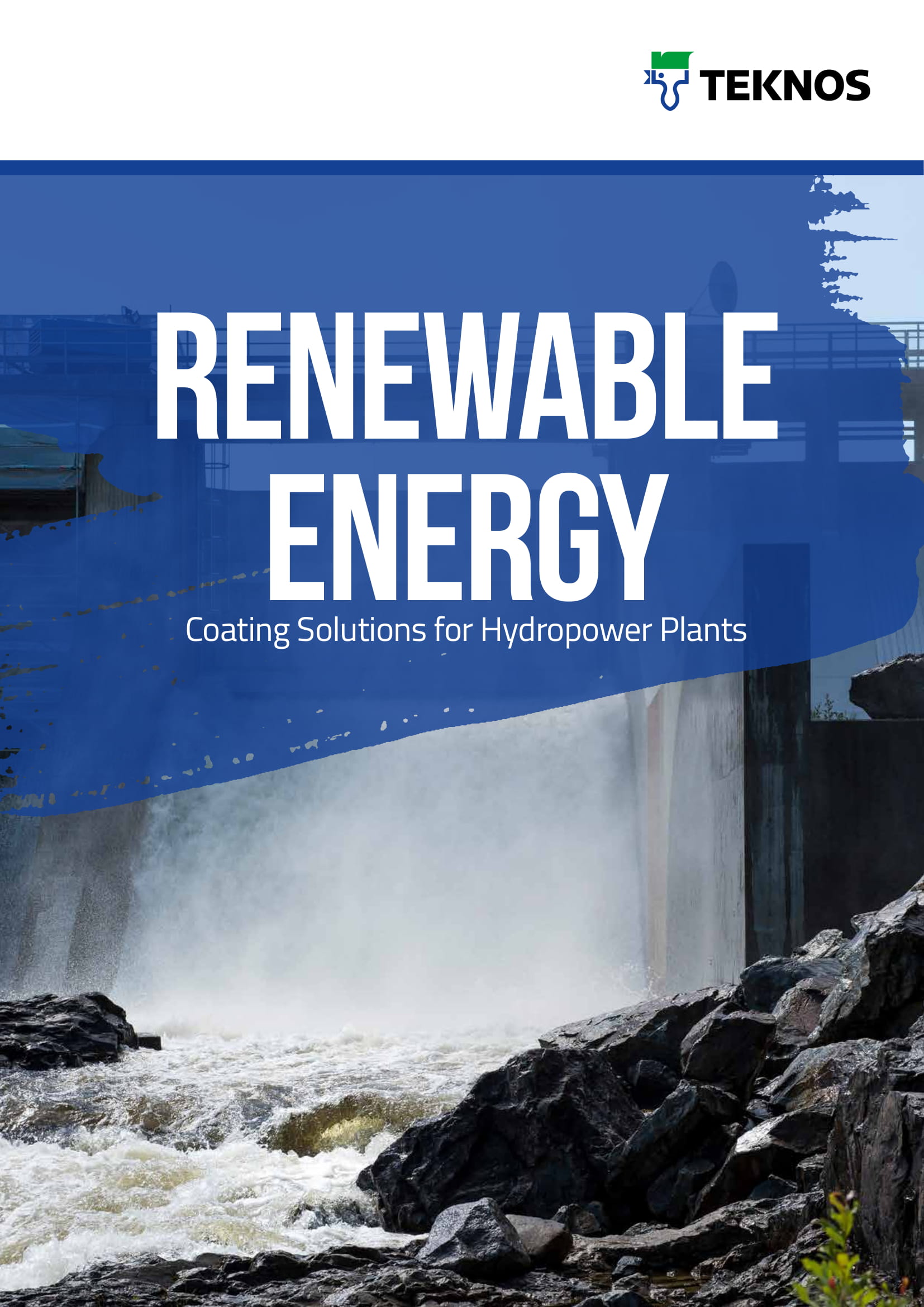