INERTA 165
Epoxy coating
- Corrosion protective
- Wear resistant
- 2-component
- Solvent-borne
- Primer
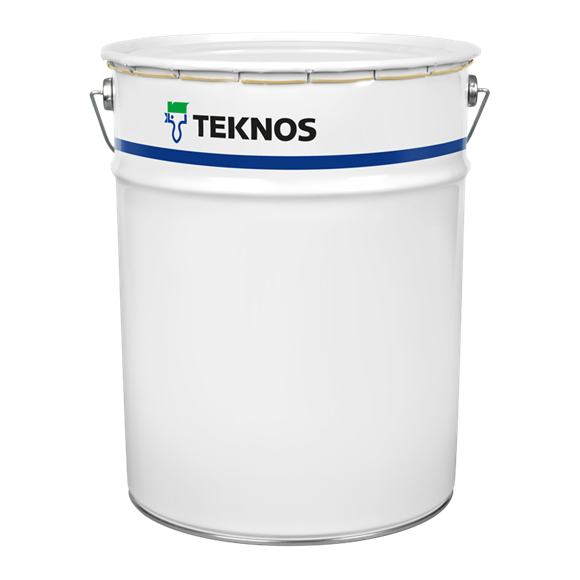
- Corrosion protective
- Wear resistant
- 2-component
- Solvent-borne
- Primer
INERTA 165 is a two-pack epoxy coating with low solvent content and based on liquid epoxy resin.
Used on steel in Epoxy coating system. Also suitable on concrete. Also used on objects immersed in water, e.g. sluice gates and pipelines of hydropower plants. INERTA 165 has good adhesion to blast-cleaned steel and excellent abrasion resistance due to smooth and hard surface of the cured film. It is therefore suitable for use on structures that are to be subjected to heavy abrasion. INERTA 165 can be applied by airless spray, either one-component or hot twin-feed spray. Also INERTA 165-02 HARDENER can be used in the product. Compared to the standard hardener INERTA 165 HARDENER it enables to shorten the curing time and to extend the pot life. In addition the spraying properties of the paint get better, it is possible to paint thicker films without sagging and the drying temperature can be +5°C.
Technical data sheet
Surface preparation
Application
Application conditions
Maintenance
Storage
Volatile organic compound (VOC) | INERTA 165 HARDENER approx. 100 g/l INERTA 165-02 HARDENER approx. 70 g/l The VOC value provided is the average value for factory produced products, and consequently it will be subject to variations between individual products covered by this Technical Data Sheet. |
---|---|
Pot life | 30 min. (+23 °C) |
Pot life, +23°C | INERTA 165 HARDENER 30 min INERTA 165-02 HARDENER 60 min |
Mixing ratio | 2:1 by volume (comp. A : comp. B) |
Hardener | Comp. B: INERTA 165 HARDENER or INERTA 165-02 HARDENER |
Gloss | Gloss |
Practical spreading rate | The values depend on the application technique, surface conditions, overspray, etc. |
Drying time – dust free | INERTA 165 HARDENER / INERTA 165-02 HARDENER 6 h / 4 h (ISO 9117-3:2010) |
Drying time – touch dry | INERTA 165 HARDENER / INERTA 165-02 HARDENER 12 h / 7 h (ISO 9117-5:2012) |
Drying time – fully cured | 7 d |
Thinner | TEKNOSOLV 9506 |
Clean up | TEKNOSOLV 9506 |
Colours | White (TM 101) and black (TM 102). Other colours with some restrictions. |
Safety markings | See safety data sheet. |